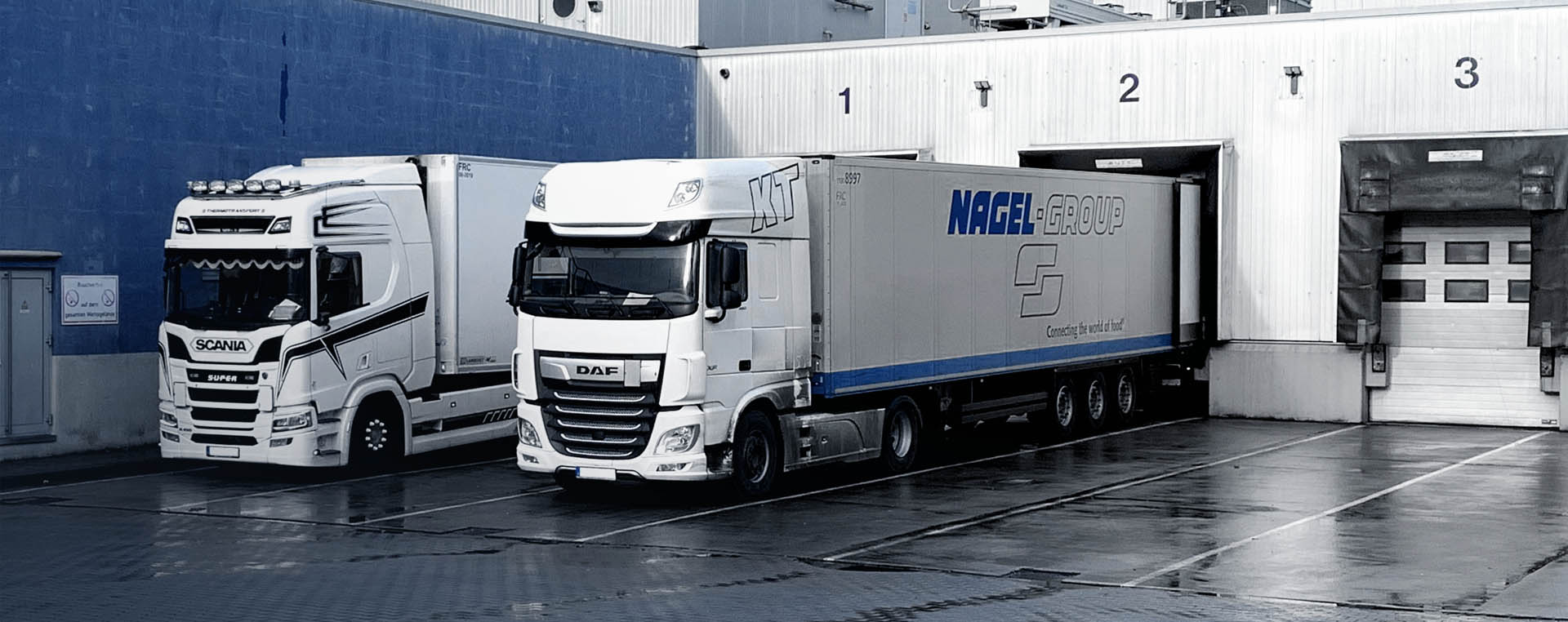
Fresh ideas for fresh products: Rücker dairy reduces waiting times at loading points
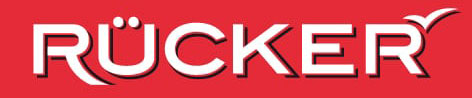
Rücker dairy has stood for northern German milk and cheese expertise for around 130 years. The family-owned company is the quality and market leader in North German naturally matured cheese specialties and supplies customers worldwide.
In order to remain fit for the future, the north German dairy Rücker took a close look at its logistics processes. This became necessary not least due to the increasing number of transports and the growing importance of the factor time in logistics. Since summer 2020, the dairy has been planning and managing its loading points with myleo / slot, the time slot management software from leogistics GmbH.
With the introduction of myleo / slot in Aurich, shipments are organized centrally and in a single system. Paper and list-based planning are now a thing of the past. For the warehouse’s schedulers, the cooperation with the forwarding companies in time slot planning enables an optimization of all gate activities.
leogistics enables help for self-help
leogistics was commissioned with the goal of enabling external service providers to book time slots independently. However, the dairy’s specialist department was to retain sovereignty over the time slot rules.
When configuring the cloud solution, leogistics worked closely with Rücker to use the “rapid approach”. This is a methodology that enables customers to put the new solution into operation largely on their own, without having to forego options for adapting it to their own processes. leogistics carried out the basic configuration for Rücker and trained the key user in myleo / slot. This laid the foundation for internal workshops, which were conducted at Rücker on its own and aimed at a final, fine-tuned configuration.
The solution at a glance
-
For Rücker, the implementation process of myleo / slot was a great success: The project was characterized by short implementation time and all wishes of the specialist department were taken into account.
-
Thanks to the intuitive user interfaces of myleo / slot, the training effort was reduced to a minimum and all parties involved were able to participate quickly.
-
External service providers have been communicating via the platform since the introduction of myleo / slot, making additional lists superfluous.
-
The utilization of resources in front of and behind the gates could be smoothed.
A look into the future
Following the successful implementation of myleo / slot, Rücker is already planning the next digitization steps. The focus here is on the exact coordination of the planned use of resources with the expected workload.
For greater efficiency and precision, process steps from the notification of the expected trucks, through dispatching, to the free notification of the gates will be carried out with myleo / yard in the future. The connection to SAP ERP is also being evaluated. This would enable the dairy to create a continuous data flow that makes manual intervention mostly obsolete due to a higher degree of automation.
Furthermore, empty and returnable packaging processing is also to be mapped via myleo / dsc in the future in order to simplify the reconciliation of credit balances or container debts of the service providers.
When it comes to fresh products, adherence to delivery dates and well-interlocked processes are essential. Delays are also critical for our customers. We are pleased to have found a tool in myleo / slot that simplifies the planning of time slots and makes any deviations transparent for all parties involved.
Klaus Rücker, Managing Director Rücker GmbH
BENEFIT FROM OUR EXPERTISE! TALK TO US.
We are happy to support you with your logistics and digitization projects.