To ensure that orders reach the end customer on time and safely, all processes in the yard must link up seamlessly. This requires that all partners - logistics service providers, suppliers and customers - work together transparently and have control over the various processes. This also includes the recording and management of all full and empty containers in which goods are transported and handled. In order not to lose track of the countless pallets, containers and the like, it is advisable to rely on specialized software that significantly simplifies the process. This not only gives companies control over administration, but also allows them to optimize their inventories, expenses and container volumes.
What Is Container Management?
In logistics, the term container management describes the information management of all containers or loading equipment that are or were used for the material flow. For shippers, it is relevant in order to carry out capacity as well as time planning for the corresponding trucks and to be able to provide concrete information for delivery and collection. Logistics service providers and freight forwarders thus obtain an overview of the quantity and characteristics of the respective load carriers. The tasks of container management range from damage control and maintenance to documentation, storage location planning and onward loading.
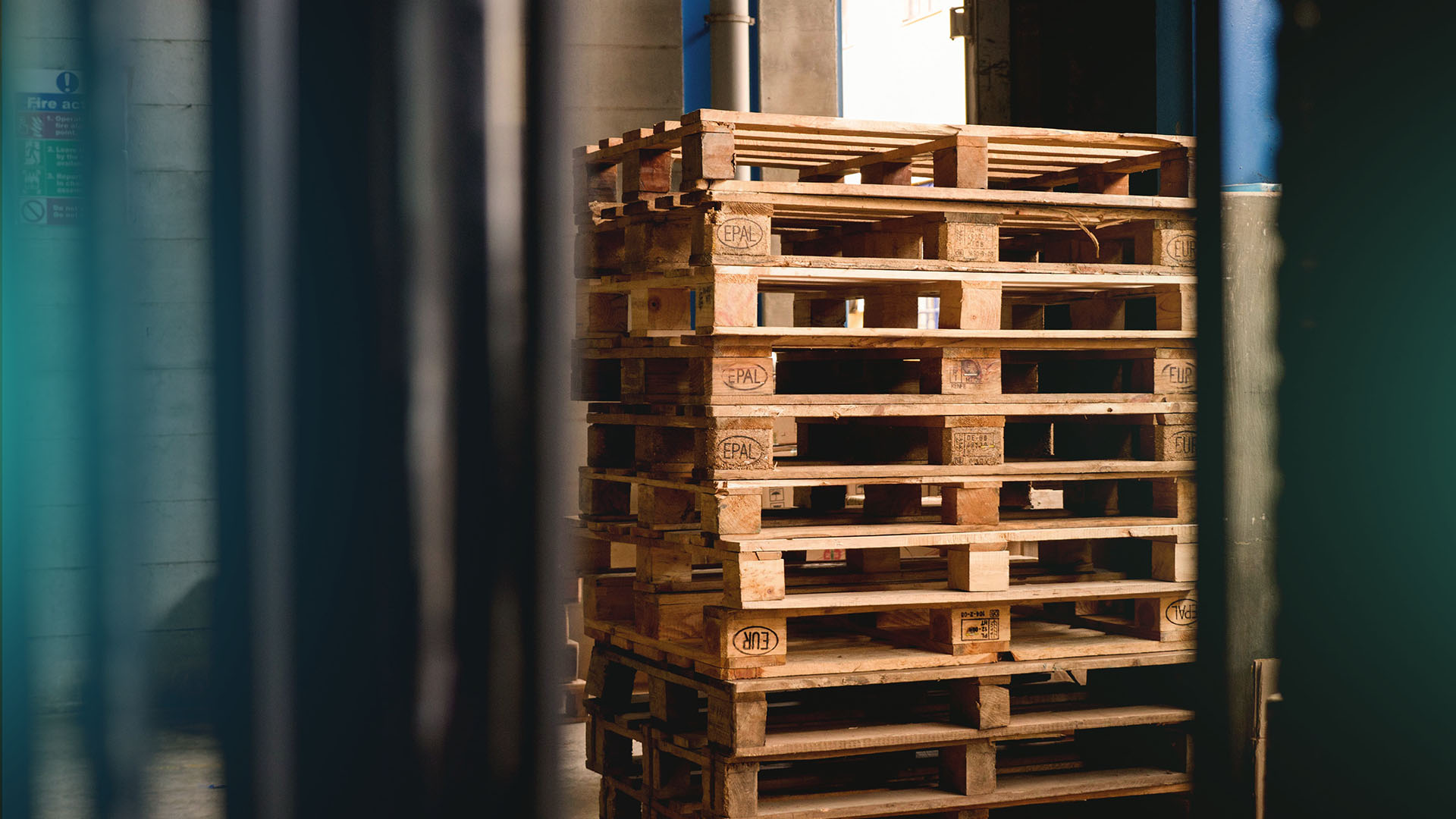
Why Is Container Management So Critical to Logistics?
Without adequate container management, serious problems arise for the entire supply chain. These may include a lack of capacity in the transport vehicles and in the service provider's warehouse, faulty planning processes or even a complete loss of control over the transport operations. This also has a negative impact on other critical processes such as appointment scheduling or vehicle management. Poor management of containers, for example, leads to significant delays in material flow and dissatisfied employees. Moreover, in case of missing or incorrect information on the part of the client, the service provider can issue a delivery ban. In summary, container management is therefore not only beneficial, but absolutely necessary.
What Needs to Be Considered in Good Container Management?
Container management is based on communication between the customer and the service provider. In addition to planning loading equipment movements and capacities, it is therefore essential for the customer to forward data such as weight, size, contents and the planned arrival time in full. This enables the carrier or logistics service provider to designate a suitable storage location for the freight at an early stage. At the same time, it is up to both parties to carry out regular quality checks and ensure seamless data management. Due to the abundance of information, however, these tasks can hardly be solved manually. The result is careless errors and loss of control, which further increases the effort required. Support is provided by container management systems, which enable effective organization of the containers and highlight additional optimization potential in the processes.
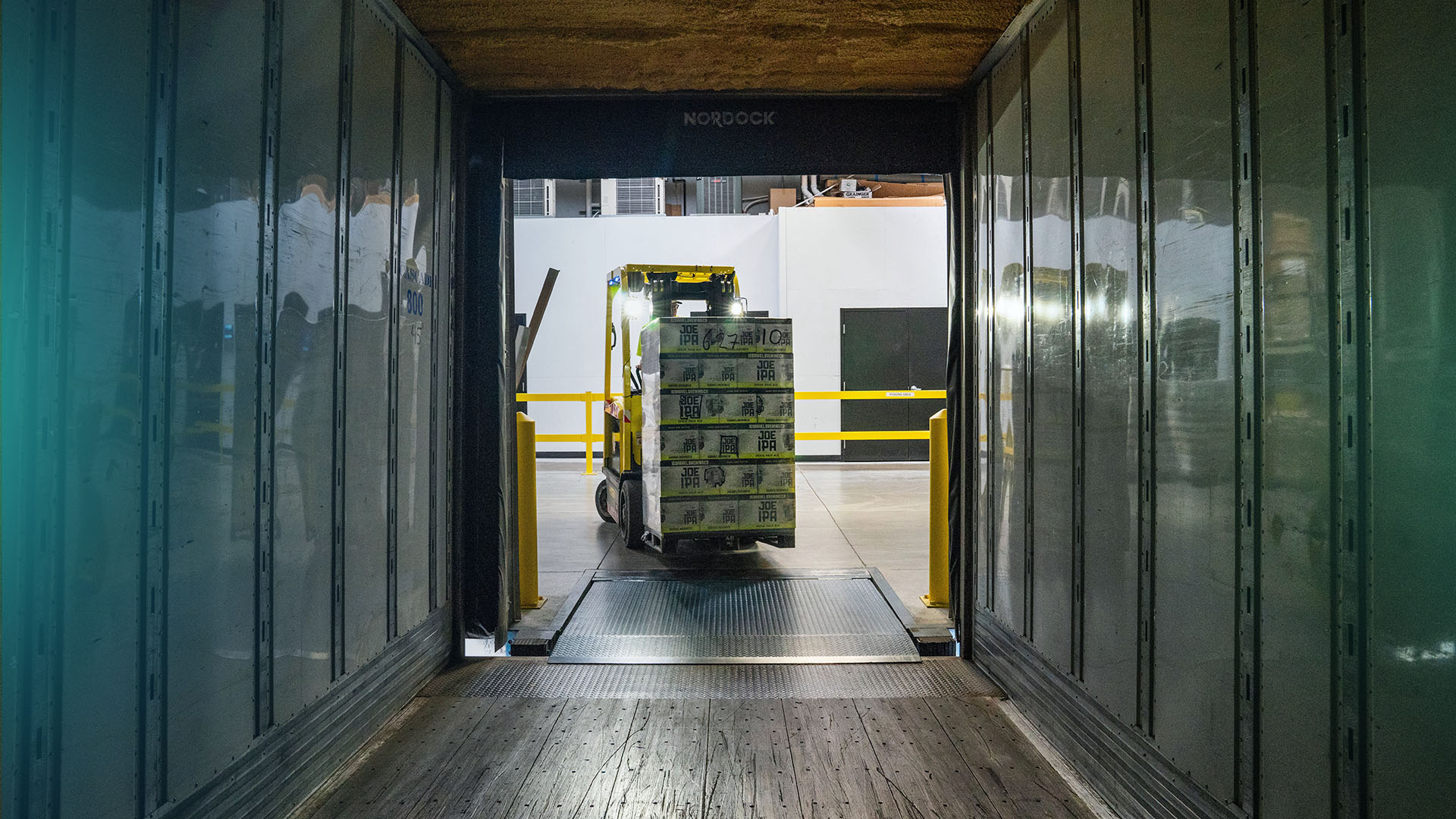
What Are the Features of Classic Container Management Software?
Container management systems free employees from a large part of the time-consuming work steps by creating transparency in all container movements within the various operations. They provide an overview of the quantities, types and current locations of the respective trailers, pallets or skeleton containers. For a comprehensive overview, advanced software uses definable loading equipment accounts within the supply chain. It records and books all loading equipment movements in the system and independently manages the corresponding container accounts. Modern programs and platforms also offer an uncomplicated communication option so that the various parties can coordinate more easily. The functions thus create a high degree of automation that significantly increases the efficiency of all processes and enables employees to manage them in a coordinated and simple manner.
Although this approach already provides a high degree of transparency, the future focus of container management software lies in the fully automated end-to-end mapping of processes and load carriers. To do this, programs must have capabilities to track containers quickly and accurately. This can be achieved with IoT (Internet of Things) technologies such as Bluetooth Low Energy (BLE) or RFID (Radio-Frequency Identification), but so far only a few systems can do this.
Benefits of myleo / dsc for Your Container Management
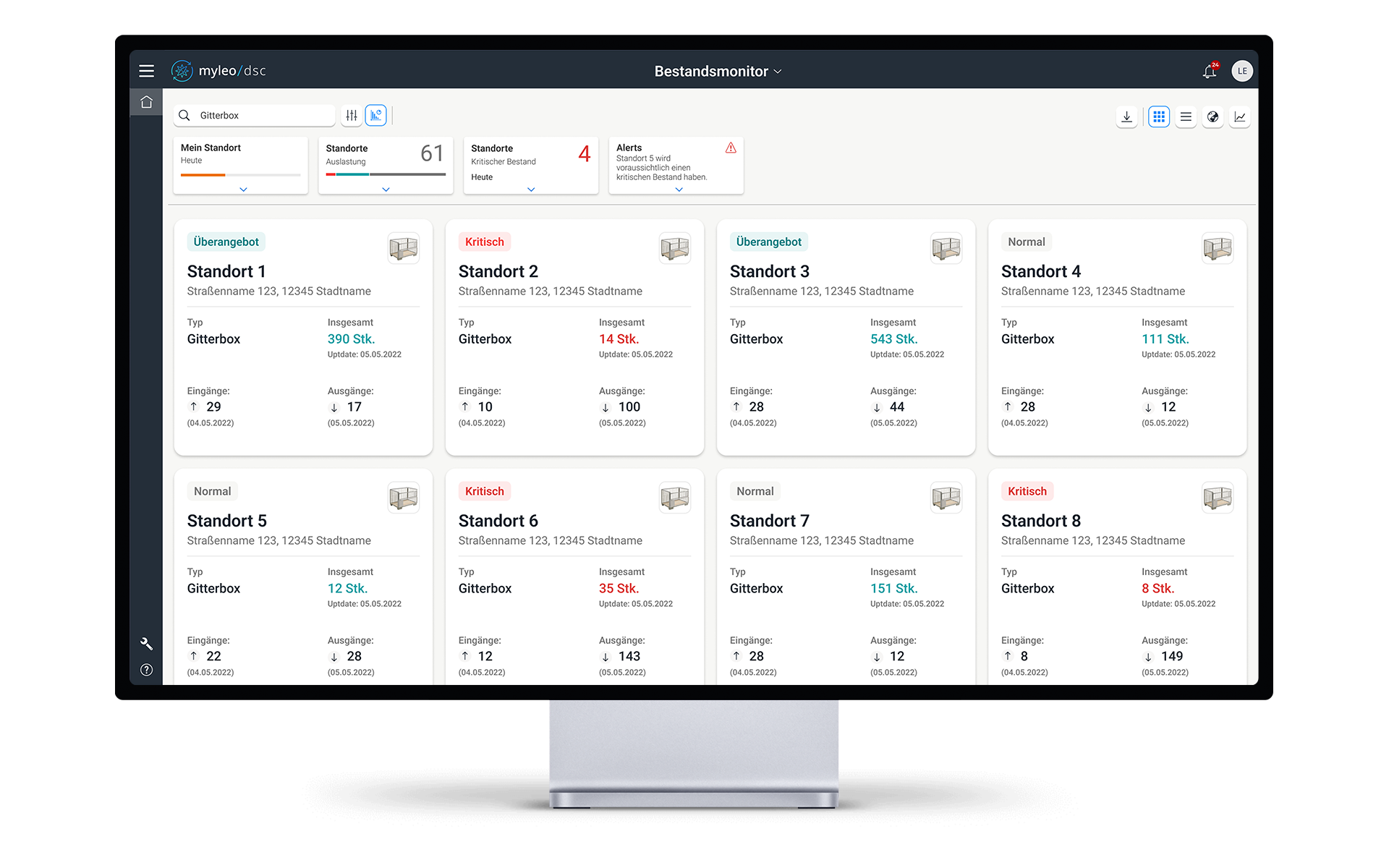
The technical prerequisites for this are provided by myleo / dsc. Our central logistics platform has many advantages over conventional container management software. It maps accounting cycles completely transparently and in real time. Both the recording and booking of incoming and outgoing goods and the reconciliation of container accounts are carried out very simply via a smartphone application. On the cloud platform, all participants in the supply chain can also view, collaborate and communicate on bookings, inventories and container locations. In addition, myleo / dsc offers further functions that simplify and optimize the management of load carriers:
- Digital pallet slips
- Data integration from pre-systems such as Oracle or SAP
- Freely configurable container types
- Mapping of individual booking behavior (e.g. according to freight order type)
With the help of myleo / dsc, it is not only easier to organize and control container cycles across different locations. At the same time, the costs and time required in all management processes are reduced. By implementing optimization suggestions, these savings can increase even further.
myleo / dsc: Process-as-a-Service for All Major Yard Processes
Container management is only one of the many disciplines in dock & yard management. myleo / dsc additionally supports companies in other sub-areas of site and transport logistics, such as transport management, appointment scheduling and ramp management. For more information on our holistic solution for your yard logistics, please visit: https://myleodsc.com/en/yard-dock-management