Inbound logistics plays a decisive role in the optimisation of supply chains. It has a major influence on the success of a company. However, inbound logistics faces major challenges: A lack of transparency and communication between suppliers and companies in inbound regularly leads to production delays and high costs. The digitalisation of inbound processes offers a pioneering solution here to optimise the supply chain and create greater efficiency. yard management
Inbound Logistics: Definition and Goals
Inbound logistics can be divided into procurement logistics and production logistics. It comprises all processes associated with the procurement, transport, receipt and storage of goods and materials along the supply chain. Its main objective is to provide production resources, containers and components on time, in the required quantity and quality in order to ensure a smooth production process and punctual goods turnover. Well-organised inbound logistics avoids idle times, optimises material flows and makes a decisive contribution to the efficiency of the entire supply chain through transparent and coordinated processes.
Inbound Logistics: What challenges need to be overcome?
An undisturbed flow of information is the backbone of properly functioning inbound logistics. However, there are often difficulties in communication between suppliers and goods recipients. This lack of transparency has far-reaching consequences. If there are delays or changes in incoming goods, this has an impact on the rest of the process. If the recipient is not informed in good time, personnel and warehouse capacities are unnecessarily blocked and waiting times occur. Unannounced deliveries also pose a problem. But there are other challenges too.
Insufficient Master Data Maintenance
Master data such as supplier data, article information, price lists and other relevant information is stored in the ERP (Enterprise Resource Planning) system. This data serves as the basis for the planning, procurement and control of inbound logistics processes. However, the ERP system often lacks detailed information on availability, price changes or the appropriate call-off quantity. This can lead to problems in order processing and delivery date management.
Missing Information on Type and Quantity of Goods
The client often only receives a confirmed delivery date, but no information about the quantity and type of goods, the means of transport or the packaging method. In practice, the recipient of the goods has to wait for the truck and only finds out exactly what is inside when the loading compartment is opened.
No Up-to-date Information on Transport
One of the key challenges in inbound logistics is the lack of transparency regarding the status of deliveries. Often, only a delivery time is communicated without current status updates or real-time information being available. As a result, companies are also unable to estimate whether the truck will arrive on time or whether delays will occur. Delayed deliveries also have far-reaching consequences for outbound transport. If materials arrive late, the timely delivery of end products can be jeopardised.
Lack of Process Visualisation
With complex supply chains in particular, it is crucial that information about the status, route and possible delays is not only available, but also clearly visualised. Without visualisation, possible deviations from planning or bottlenecks cannot be identified in good time.
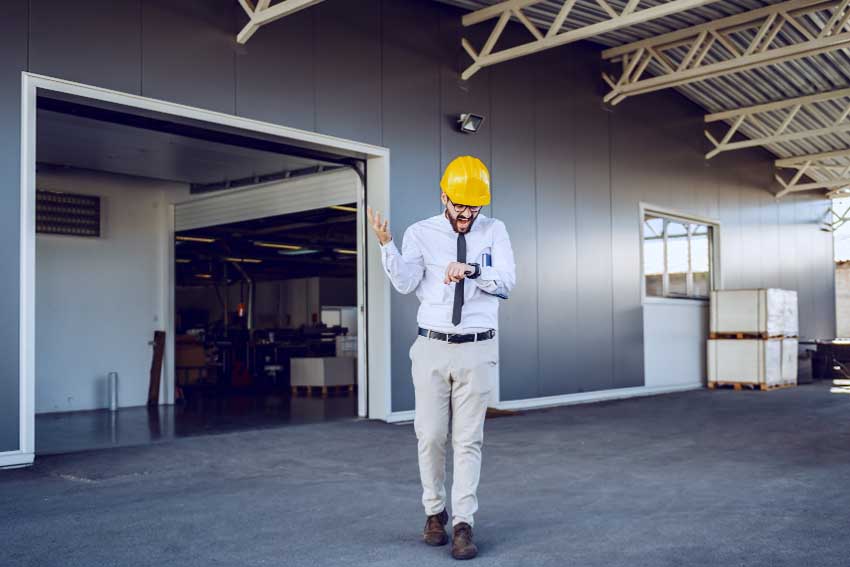
A Negative Example from the Field
The worst case has happened: A truck loaded with urgently needed goods has crashed. The haulier, overwhelmed by the situation, fails to inform the client of the incident. Instead, he sends a replacement lorry to make up the delivery as quickly as possible. Meanwhile, the client continues to expect the delivery within the agreed time frame - but in vain. The new lorry arrives at the logistics depot almost three hours late. At this point, however, the originally reserved storage space is already occupied by someone else, which further delays acceptance of the delivery. This example illustrates how a lack of communication can lead to avoidable disruptions. The delay caused by the accident is regrettable, but the supply chain is by no means interrupted as a result. With proactive and transparent communication, the freight forwarder could have informed the shipper in good time so that they could have kept the storage space free and accepted the delivery later.
Solution: Digitalisation of Inbound Logistics
The digitalisation of inbound logistics offers an effective answer to the numerous challenges that companies face in this area. By using modern software solutions, processes can be optimised, resources can be saved and collaboration between partners along the supply chain can be significantly improved.
Features of Suitable Software
1. Options for tracking goods and transport
A central function of digital solutions is the tracking of deliveries in real time. This allows companies to know where their goods are at all times and recognise delays or problems at an early stage. Live tracking makes it possible to directly identify deviations in the delivery schedule and initiate measures to protect operations and subsequent outbound processes.
2. Documentation of information and processes
Modern software documents all information and process steps along the supply chain. From order confirmation to loading and arrival at the destination, all relevant data is automatically recorded. This not only ensures transparent traceability, but also serves as a basis for future optimisation.
3. Sending status messages
Automated status messages are an important function for keeping all parties involved continuously informed about progress and possible changes. These notifications can include delays, arrival times or other relevant events and enable companies to react flexibly to new circumstances.4. Uncomplicated communication between partnersAn integrated communication platform simplifies collaboration between suppliers, forwarders and consignees. Instead of having to use emails or phone calls, all parties can interact directly with each other. This reduces misunderstandings and speeds up coordination.
4. Uncomplicated communication between partners
An integrated communication platform simplifies collaboration between suppliers, forwarders and consignees. Instead of having to use emails or phone calls, all parties can interact directly with each other. This reduces misunderstandings and speeds up coordination.
5. Integration of upstream systems such as ERP
A good software solution should be able to be seamlessly integrated into existing upstream systems such as ERP systems. This ensures that relevant data such as orders, demand forecasts or delivery schedules are automatically transferred and processed. This minimises manual input and reduces errors.
Benefits of Seamless Inbound Processes
If inbound logistics can run according to plan, there are many advantages for the shipper, supplier and freight forwarder:
Transparent Processes
A transparent inbound process provides a comprehensive overview of the workflows. All participants are informed immediately of any changes.
Planning Reliability
Planning security also goes hand in hand with an increase in performance: companies can plan their personnel and resources in advance and optimise them for the tasks ahead.
Happy Employees and Customers
If the announced delivery arrives too late or not at all, the employees have turned up for work for nothing and the customer is also waiting in vain for their order. In turn, premature receipt of goods causes stress at the logistics centre. The situation is different with scheduled inbound logistics. This allows staff to finish work on time and the customer receives their goods on the promised delivery date.
New Optimisation Potential
In a smooth supply chain, it quickly becomes clear in which process steps there are delays despite the otherwise problem-free process. Tracking and evaluating these delays can help to identify new potential for optimisation that previously remained hidden under the logistics chaos.
More Flexible Workflows
Fluctuating market conditions and seasonality require maximum flexibility in logistics. Without the necessary overview of their own supply chain, including procurement, receipt and storage, companies are unable to react in good time to everyday changes in the market. Conversely, first-class management of your own inbound logistics improves your competitiveness.
Safety Through Quality Control
We've all been there: the delivery is damaged and the blame is quickly shifted to the other party. Instead, early quality control and documentation of the process steps help to trace the damage quickly and reliably.
Stronger Supplier Relationships
Reliable planning not only has advantages for the shipper. Delivery drivers can also set off on time for their next order without long waiting times. Seamless inbound processes save time and money for everyone involved and strengthen the business relationship.
Optimised Inbound Logistics with myleo / dsc
As a collaborative platform, myleo / dsc combines all the key functions for managing inbound logistics. This ensures efficiency. The supply chain partners can exchange information as quickly as possible in the form of digital status messages or order enquiries. The system visualises the current process flows for each user so that it is clear where the delivery is currently located. To this end, myleo / dsc offers comprehensive tracking overviews for road and rail transport. In addition, all established upstream systems such as SAP or Oracle can be easily integrated into the software. This means that the system can not only pull the required data automatically, but also provides an essential basis for detailed tracking of the pre-, main or on-carriage. This means that efficient outbound logistics can be seamlessly integrated.
As a service provider, myleo / dsc also supports its customers with its many years of expertise in the field of interfaces.
Do you want to sustainably strengthen your inbound logistics with myleo / dsc? You can find more information about our yard management solution here: https://myleodsc.com/de/yard-management